Process Engineer
Unilever
Date: 2 weeks ago
City: Boksburg, Gauteng
Contract type: Full time
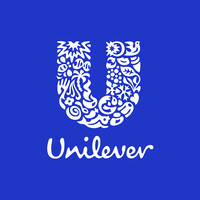
About Unilever
With 3.4 billion people in over 190 countries using our products every day, Unilever is a business that makes a real impact on the world. Work on brands that are loved and improve the lives of our consumers and the communities around us. We are driven by our purpose: to make sustainable living commonplace, and it is our belief that doing business the right way drives superior performance. At the heart of what we do is our people – we believe that when our people work with purpose, we will create a better business and a better world.
At Unilever, your career will be a unique journey, grounded in our inclusive, collaborative, and flexible working environment. We don’t believe in the ‘one size fits all’ approach and instead we will equip you with the tools you need to shape your own future.
Job Purpose
Unilever is the place where you can bring your purpose to life with the work that you do – creating a better business and a better world.
The Process Engineer role is critical to the development of our factories to World Class Manufacturing, which means zero defects, zero waste and zero losses. Lead Quality Improvement methods and tools to counter losses identified in the areas of Safety, Quality, Cost Deployment, Customer Service and Logistics. The Cost Deployment pillar will be populated with data built up through application of the Managing Manufacturing Performance Code, which is key to ensuring focus on key losses.
Working directly with the line crews on a daily basis. Act as the technical trainer for line teams and provides coaching in phenomena identification, root cause analysis and the establishment of counter-measures. Responsible for the validation of all process improvements and the establishment of revised basic conditions on the line. A core deliverable is eliminating losses and wastes and increase the stability of the line to support the transition of traditional line teams to semi-autonomous teams.
What Will Your Main Responsibilities Be
Experiences & Qualifications
Unilever is an organisation committed to equity, inclusion and diversity to drive our business results and create a better future, every day, for our diverse employees, global consumers, partners, and communities. We believe a diverse workforce allows us to match our growth ambitions and drive inclusion across the business. At Unilever we are interested in every individual bringing their ‘Whole Self’ to work and this includes you! Thus if you require any support or access requirements, we encourage you to advise us at the time of your application so that we can support you through your recruitment journey.
With 3.4 billion people in over 190 countries using our products every day, Unilever is a business that makes a real impact on the world. Work on brands that are loved and improve the lives of our consumers and the communities around us. We are driven by our purpose: to make sustainable living commonplace, and it is our belief that doing business the right way drives superior performance. At the heart of what we do is our people – we believe that when our people work with purpose, we will create a better business and a better world.
At Unilever, your career will be a unique journey, grounded in our inclusive, collaborative, and flexible working environment. We don’t believe in the ‘one size fits all’ approach and instead we will equip you with the tools you need to shape your own future.
Job Purpose
Unilever is the place where you can bring your purpose to life with the work that you do – creating a better business and a better world.
The Process Engineer role is critical to the development of our factories to World Class Manufacturing, which means zero defects, zero waste and zero losses. Lead Quality Improvement methods and tools to counter losses identified in the areas of Safety, Quality, Cost Deployment, Customer Service and Logistics. The Cost Deployment pillar will be populated with data built up through application of the Managing Manufacturing Performance Code, which is key to ensuring focus on key losses.
Working directly with the line crews on a daily basis. Act as the technical trainer for line teams and provides coaching in phenomena identification, root cause analysis and the establishment of counter-measures. Responsible for the validation of all process improvements and the establishment of revised basic conditions on the line. A core deliverable is eliminating losses and wastes and increase the stability of the line to support the transition of traditional line teams to semi-autonomous teams.
What Will Your Main Responsibilities Be
- Eliminate Waste and Loss according to the WCM prioritization process using AM, PM, FI and QC pillar tools and methodologies.
- Create Technical and Quality Standards to ensure process stability on the line.
- Identify and extend good practice to other lines.
- Application and accuracy of MMP Code data
- Consumer and Customer Focus:
- Building world class factories will eliminate losses and ensure that we do not pass on the cost of inefficiencies to our customers and consumers
- Bias for Action:
- By providing consistent and near real time information, decisions can be taken quickly which leverage our resources
- Building Talent and Teams:
- Our vision is to move to semi-autonomous teams.
- Passion for achieving results.
- Transfer knowledge and skills across the team and leverage team strengths
- Accountability and Responsibility:
- Drive continuous improvements.
- Growth Mindset:
- By building world class factories essential to set the standards
- WCM:
- Apply the full set of WCM methods and tools.
- Process and Organisational Design:
- Ensure factory lines and processes are optimally resourced (e.g. manpower ratios are efficient and sustainable)
- Analytical capability:
- Collect and analyse and interpret complex data.
- Understanding and implementation of process safety requirements for combustible dusts.
- Run engineering projects:
- New equipment or optimization of current equipment to maximise the efficiency of the factory and bring savings into the business
- Land Innovations in the factory to drive the business forward and bring in cost savings that improve the gross margin.
- Debottle and otpimise the current processes to maximise output and reduce cost.
Experiences & Qualifications
- Degree/ BTech Mechanical/ Chemical/ Industrial Engineering/ National Diploma Chemical Engineering
- Experience from a Continuous Processing background within FMCG or Manufacturing environment will be advantageous
- Experience in packing line technology and optimization of packing lines.
- Experience in AM, PM, Quality and FI tools and processes.
- Experience in landing engineering projects.
- HAZOPs and Safety Approval Systems working knowledge and experience is essential
- Able to visualize clearly what the ideal production system should be.
- Clearly understand operating principles and establish correct operating standards
- Experience in statistics and process control tools. Drive decision making based on data
- Process Engineering
- Design & Automation
- Process Safety & Control
- Innovation & improvement
- You are energized by delivering fantastic results. You are an example to others – both your results and your resilience. You are constantly on the lookout for better ways to do things, engaging and collaborating with others along the way.
- As an individual you are the one responsible for your own wellbeing and delivering high standards of work. You must also focus on the Consumer and what they need. You are humble and have your head up, looking around to interpret evidence and data smartly, spot issues and opportunities to make things better.
- Critical SOL (Standards of Leadership) Behaviors
- PASSION FOR HIGH PERFORMANCE: Takes personal responsibility and accountability for execution and results. Has an owner’s mindset, using data and insight to make decisions.
- PERSONAL MASTERY: Sets high standards for themselves. Actively builds own wellbeing and resilience.
- CONSUMER LOVE: Whatever their role, always looks for better ways to serve consumers. Invests time inside and outside to understand the needs of consumers.
- PURPOSE & SERVICE: Has humility, understanding that leadership is service to others, inside and outside Unilever.
- AGILITY: Explores the world around them, continually learning and developing their skills.
Unilever is an organisation committed to equity, inclusion and diversity to drive our business results and create a better future, every day, for our diverse employees, global consumers, partners, and communities. We believe a diverse workforce allows us to match our growth ambitions and drive inclusion across the business. At Unilever we are interested in every individual bringing their ‘Whole Self’ to work and this includes you! Thus if you require any support or access requirements, we encourage you to advise us at the time of your application so that we can support you through your recruitment journey.
See more jobs in Boksburg, Gauteng