Production Manager at Rhodes Food Group
RFG Foods
Date: 10 hours ago
City: Johannesburg, Gauteng
Contract type: Full time
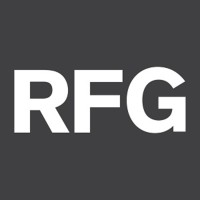
Introduction
Direct and coordinates activities concerned with production of company product. Confers with management to establish production and quality control standards, develop budget and cost controls and to obtain data regarding types, quantities, specifications, and delivery dates of products ordered. Plans and directs production activities and establishes production priorities for products in keeping with effective operations and cost factors. Plans and coordinates production activities to obtain optimum production and utilization of human resources, machines and equipment.
Duties & Responsibilities
Manage production activities in a high-pressured environment.
Ensure smooth operation of various activities in the factory.
Plan and coordinate shift activities to meet overall production and Company objectives.
Ensure production plan is met as per requirements with the required yield.
Manage packaging and machine material interaction.
Lead, control and conduct training for the production team.
Motivate and monitor team to achieve their operational targets.
Ensure materials and expenses are in order.
Responsible for the care of assets.
Maintain operating expenses to be in line with budget including labour, consumables and other items within specified control.
Take corrective action on any audit findings for the facility.
Ensure raw materials required for the production plan are available and report any shortages timeously to mitigate risk to the business. Take for corrective action as required.
Ensure facility infrastructure and equipment are taken care of and action is taken where there are none conformances noted.
Deploy people management processes - workforce planning, recruitment and selection, learning and development, performance management and employee relations etc. effectively, in line with organisational policies, procedures and prevailing improvement initiatives.
Manage the working environment and ensure it contributes to improving staff morale and increasing productivity.
Design and review operation's organisational structure to support operational plans and strategy, in collaboration with HR.
Manage budgets and monitor expenses ensuring expenditure is within the budget.
Manage and strive to eliminate internal rejections and waste
Ensure production variances are under control and within recovery as per the budget, correct where there are high losses.
Continuously strive to save costs.
Monitor any trends in food and operational safety compliance issues and proactively address to resolve.
Actively address all customer and supplier concerns.
Adhere to, and lead in the compliance of all Environmental, Health and Safety and all other applicable regulatory statutes, and all other safety and quality systems.
Proactively identify continual improvement strategies.
Action agreed quality initiatives ensuring that they are aligned to tasks/ processes/ systems.
Implement corrective actions identified within specified time.
Ensure compliance with product quality standards.
Ensure hygiene and housekeeping is maintained at required levels for readiness of any food hygiene/ safety audit.
Carry out internal facility audits as specified by the Quality Management (QM) system.
Report on production variances and efficiencies.
Develop and submit processing reports required by the operations team.
Desired Experience & Qualification
Direct and coordinates activities concerned with production of company product. Confers with management to establish production and quality control standards, develop budget and cost controls and to obtain data regarding types, quantities, specifications, and delivery dates of products ordered. Plans and directs production activities and establishes production priorities for products in keeping with effective operations and cost factors. Plans and coordinates production activities to obtain optimum production and utilization of human resources, machines and equipment.
Duties & Responsibilities
- Production Management
Manage production activities in a high-pressured environment.
Ensure smooth operation of various activities in the factory.
Plan and coordinate shift activities to meet overall production and Company objectives.
Ensure production plan is met as per requirements with the required yield.
Manage packaging and machine material interaction.
Lead, control and conduct training for the production team.
Motivate and monitor team to achieve their operational targets.
Ensure materials and expenses are in order.
Responsible for the care of assets.
Maintain operating expenses to be in line with budget including labour, consumables and other items within specified control.
Take corrective action on any audit findings for the facility.
Ensure raw materials required for the production plan are available and report any shortages timeously to mitigate risk to the business. Take for corrective action as required.
Ensure facility infrastructure and equipment are taken care of and action is taken where there are none conformances noted.
- People Management
Deploy people management processes - workforce planning, recruitment and selection, learning and development, performance management and employee relations etc. effectively, in line with organisational policies, procedures and prevailing improvement initiatives.
Manage the working environment and ensure it contributes to improving staff morale and increasing productivity.
Design and review operation's organisational structure to support operational plans and strategy, in collaboration with HR.
- Financial Management
Manage budgets and monitor expenses ensuring expenditure is within the budget.
Manage and strive to eliminate internal rejections and waste
Ensure production variances are under control and within recovery as per the budget, correct where there are high losses.
Continuously strive to save costs.
- Health and Safety/Governance and Compliance
Monitor any trends in food and operational safety compliance issues and proactively address to resolve.
Actively address all customer and supplier concerns.
Adhere to, and lead in the compliance of all Environmental, Health and Safety and all other applicable regulatory statutes, and all other safety and quality systems.
- Quality
Proactively identify continual improvement strategies.
Action agreed quality initiatives ensuring that they are aligned to tasks/ processes/ systems.
Implement corrective actions identified within specified time.
Ensure compliance with product quality standards.
Ensure hygiene and housekeeping is maintained at required levels for readiness of any food hygiene/ safety audit.
Carry out internal facility audits as specified by the Quality Management (QM) system.
- Administration
Report on production variances and efficiencies.
Develop and submit processing reports required by the operations team.
Desired Experience & Qualification
- Matric
- Diploma in Production or Operations Management, business administration, management, engineering, industrial technology an advantage.
- knowledge and experience in production and manufacturing processes and techniques
- knowledge of raw materials
- knowledge of quality systems and standards
- knowledge of health and safety standards and compliance
- knowledge of process improvement techniques
- knowledge of business, finance and management principles
- knowledge of human resource principles and practices
- knowledge of machines and tools
- knowledge of engineering and technology principles and practices
- solid computer skills
- Excellent communication skills
- Leadership and interpersonal skills
- Problem solving skills
- Teamworking skills
- Organization and efficiency
- 4-6 years' experience
- Knowledge of Food Safety and HACCP Principles.
See more jobs in Johannesburg, Gauteng